ICPS 2025 Industry Forum (IF)
The Industry Forum (IF) has been organized for several years in major IEEE IES events. The Industry Forum features Industry speakers discourcing on the conference themes.
The Industry Forum at the 8th IEEE Conference on Industrial Cyber-Physical Systems (ICPS) serves as a vital bridge between academia and industry, fostering discussions on the latest innovations, challenges, and trends in ICPS applications. This forum brings together leading experts, researchers, and practitioners to explore real-world deployments, emerging business opportunities, and the evolving landscape of cyber-physical technologies across various sectors, including manufacturing, logistics, and the circular economy.
The ICPS 2025 Industry Forum is taking place throughout all four conference days. A dedicated timeslot each afternoon has been reserved for the Industry Forum to enable as many of the conference participants as possible to engage in the talks and discussions.
In up to two parallel sessions each day, the Industry Forum will provide insights from Industry experts in the following areas:
- IF Session 1: Data Platforms – Challenges, Best Practices and Benefits
- IF Session 2: Digitalization in the Circular Economy and Logistics – Regional Solutions for a Sustainable Future
- IF Session 3: Production from Europe
IF Session 1: Data Platforms – Challenges, Best Practices and Benefits
Tuesday, 13th May 2025, 13:00–15:00
Chairs: Christoph Wunck, Stamatis Karnouskos
Session Theme: In an era defined by data-driven transformation, modern enterprises rely on data platforms as the foundation for analytics, AI, and operational efficiency. This session will examine the key challenges organizations face in building and maintaining scalable, secure, and high-performing platforms, including fragmented data landscapes, evolving compliance requirements, and infrastructure complexity. The discussion will highlight industry best practices for platform architecture, data governance, and cloud integration, as well as the strategic benefits gained through enhanced agility, real-time insights, and improved decision-making. Designed for technology leaders and data professionals, this session offers practical insights into aligning data platform strategies with business objectives in an increasingly complex digital environment.
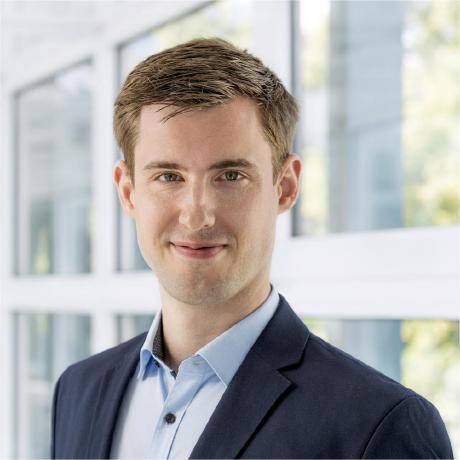
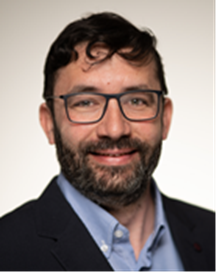
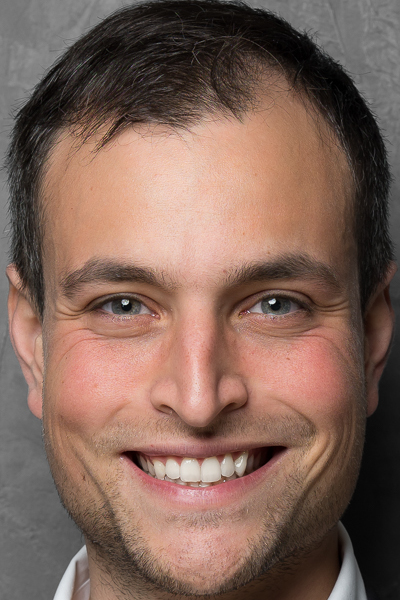
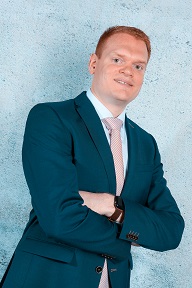
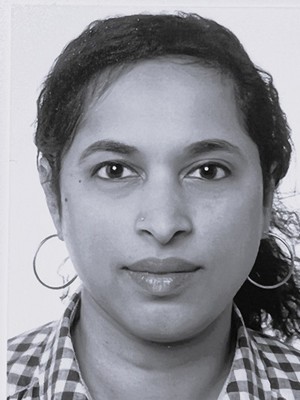
Talk: Bridging Industries: Aerospace-X as a Digital Data Ecosystem in Aviation based on Results from the Automotive Data Ecosystem Catena-X
Marvin Manoury Fraunhofer IPK
Abstract: In today’s world, the aviation industry is increasingly shaped by digital transformations. The first operational data ecosystem in the automotive industry, Catena-X, has paved the way for innovative approaches. Within the framework of Manufacturing-X, numerous other data ecosystems are currently emerging, aimed at enhancing efficiency and transparency across various industries. One of these data ecosystems is Aerospace-X, specifically designed for aviation. This presentation highlights the current challenges faced by companies in transferring automotive solutions to aviation, particularly regarding regulatory requirements. Additionally, the current status of the Aerospace-X data ecosystem will be presented to showcase how this approach could revolutionize the aviation industry and the potential it holds for the future.
Speaker Bio: As a researcher at Fraunhofer IPK in the Department of Sustainable Product Ecosystems, Marvin Manoury focuses on analyzing the product lifecycle and the consistency of information related to products throughout this lifecycle. His particular emphasis is on digital twins, which play a crucial role in the optimization and traceability of products. These are utilized in the Aerospace-X project for describing all forms of products and materials. He is particularly focused on developing a digital architecture to achieve this consistency within the data ecosystem. Additionally, he serves as the lead in the Catena-X association within the DPP working group, transferring these insights into the Aerospace-X initiative.
Talk: DAVID: Advancing Interoperable Data Spaces in Manufacturing-X
Alfred Barnard ifak Institut für Automation und Kommunikation e.V.
Abstract: The DAVID project (“Digitale Administration industrieller Wertschöpfung durch interoperable Datenräume”) is a key initiative within Germany’s Manufacturing-X program, funded by the Federal Ministry for Economic Affairs and Climate Action (BMWK). It aims to build a standardized, interoperable data ecosystem for the manufacturing sector, centered around the Asset Administration Shell (AAS). DAVID supports the harmonization of AAS submodels to enable seamless data exchange and digital representation of industrial assets across value chains. A major focus lies in empowering small and medium-sized enterprises (SMEs) with tools and interfaces that simplify access to data spaces. The project connects research, standardization, and practical implementation, fostering scalable and reusable solutions for Industry 4.0 applications across domains.
Speaker Bio: Alfred Barnard is an electrical engineer working at the Institute for Automation and Communication (ifak) in Magdeburg. He is actively involved in Industry 4.0 research projects, including DAVID and ROBOT-X, focusing on digital twins, data interoperability, and manufacturing ecosystems within the Manufacturing-X framework.
Talk: HealthTrack-X: Trailblazer of a Digitalized Supply Chain for the Industrial Healthcare Sector
Ege Hüsemoglu Bundesverband der Deutschen Industrie e.V.
Abstract: The industrial healthcare sector is facing major challenges: a lack of standards, a lack of interoperability, and little digital networking along the production and supply chain. The HealthTrack-X consortium project aims to change this. Eight partners from industry and associations are developing an interoperable, secure data space that increases the resilience, efficiency, and sustainability of the supply chain. The presentation provides an insight into the three central use cases - electronic delivery documents, data-based bottleneck prevention, and carbon footprint management - and presents initial findings. It also discusses how technical, organizational, and political hurdles can be overcome and what role the exchange with other Manufacturing-X projects plays in this.
Speaker Bio: Ege Hüsemoglu is a consultant for the industrial healthcare sector at the BDI and is responsible for the BMWK-funded HealthTrack-X project. He previously worked in communications at Roche Pharma and gained research experience at the University of Freiburg. With expertise in public affairs, project management, and communication, he has in-depth knowledge of dealing with complex stakeholder landscapes. He is a member of the Manufacturing-X Guidance Board and is involved in several expert committees.
Talk: Disaster Management & Recovery: Requirements, Industry Standards and Challenges
Gowry Sritharan Lufthansa Industry Solutions GmbH
Abstract: Disaster Management & Recovery is more than just a technical challenge—it is a cross-functional necessity. This talk outlines the core principles of disaster recovery and emphasizes the growing importance of non-technical factors such as leadership, communication, and decision-making. Using examples from HR, aviation, and operations, we explore sector-specific challenges: How can HR teams support employees under stress? What regulatory and operational issues impact aviation during IT failures? And how can operations stay flexible in times of disruption? The session highlights how Business Continuity Planning (BCP) serves as a key enabler, helping organizations recover effectively. We’ll share best practices, real-life case studies, and lessons learned that have successfully navigated crises, demonstrating what truly makes a business resilient.
Speaker Bio: Consultant at Lufthansa Industry Solutions since 2008 with experience in IT process management, SAP HCM, service management, cloud migration, and business continuity.
Talk: Driving Engineering Success with Modern Data Platforms
Carsten Manske KPMG AG
Abstract: The Future of Production Planning with Modern Data Platforms In our presentation, KPMG will showcase the capabilities that SAP Business Data Cloud offers as a modern data platform for manufacturing companies. Learn how this technology creates a trusted source for all company data and supports your production processes. Why should you attend?
- Integration of Data Sources: Discover how you can seamlessly integrate data from various systems to gain a comprehensive view of your production processes and make informed decisions.
- Ad-hoc Analyses: Learn how to quickly and flexibly respond to changing requirements. Create customized analyses in real-time and gain valuable insights.
- Planning of Production Processes: Optimize your production planning and avoid bottlenecks. With SAP Business Data Cloud, you can precisely plan and control your processes.
Speaker Bio: Carsten Manske is a Senior Manager at KPMG and has been supporting companies with digital transformation in the area of data & analytics for over 10 years.
IF Session 2: Digitalization in the Circular Economy and Logistics – Regional Solutions for a Sustainable Future
Tuesday, 13th May 2025, 13:00–15:00
Chair: Andre Wessels
Session Theme: In this session, you will gain exclusive insights into how regional companies are successfully implementing sustainable production and the circular economy. Find out how resource-saving processes, intelligent recycling and optimized value chains lead to long-term competitive advantages. At the same time, you will learn about innovative logistics solutions that companies are using to meet the challenges of digital transformation. You can look forward to best practices, current projects and exciting contacts from the region.
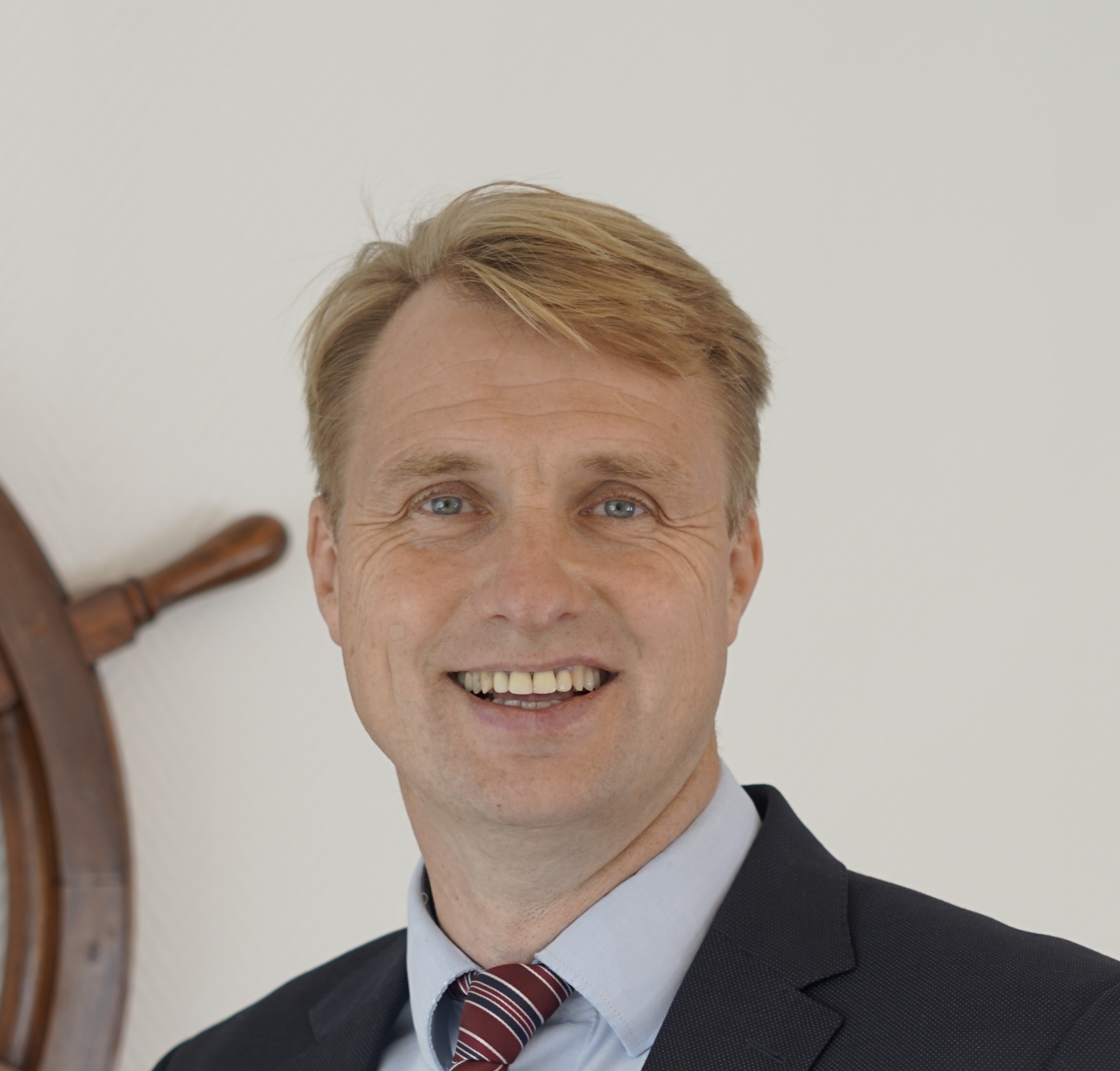
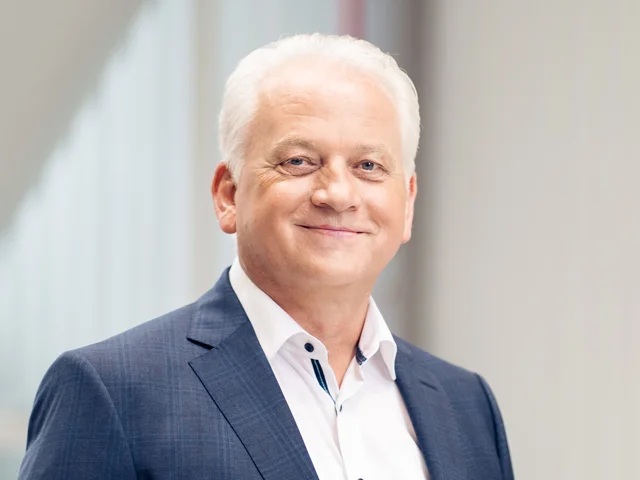
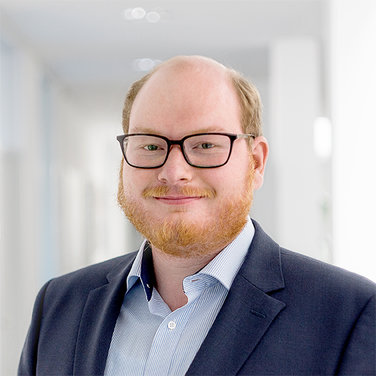
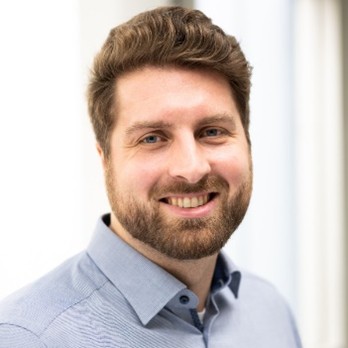
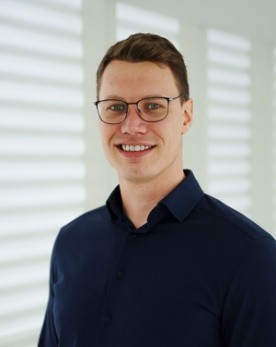
Talk: Digitizing Circular Economy
Jens Duin SYNQONY Group
Abstract: To many people circular economy is just a buzzword. But it’s a growing market with many changes for waste management companies. In one sentence: It’s not waste, it’s a resource.
This changes not only how we work together, but also who works together. At the same time, companies are facing an ongoing process of digital transformation.
Which role does a software company play in this dynamic world?
Speaker Bio: Jens Duin hold(s) a Diploma in Business Administration from the University of Applied Sciences in Emden, obtained in 1999 when the institution was known as Fachhochschule Ostfriesland. In 2000, he founded his first company, focusing on web development and marketing, while in 2018 S&F Software was successfully acquired. Since 2023, he has been dedicated to the development the SYNQONY Group.
Talk: Digital Transformation for Greater Resource Efficiency (Digi-Ress)
Hartmut Schoon Enneatech AG
Abstract: Enneatech AG is constantly working to further improve our eco-balance and the quality of our recyclates. In addition to optimized material formulations and more efficient production processes, it is becoming increasingly clear that digitalization is opening up new potential for saving resources and reducing CO₂ emissions. We are focusing on digital technologies to make processes more sustainable, transparent and efficient. The core idea of the Digi-Ress project is the complete digital mapping of the production process. By using state-of-the-art technologies, inefficient sub-processes can be identified, analyzed, and optimized based on data. In addition, an intelligent expert system was developed that automatically creates recipe specifications for recyclates. This enables more precise raw material utilization, improves product quality, and reduces energy consumption and material waste.
Speaker Bio: Hartmut Schoon is one of the founders and, since 2019, CEO of Enneatech AG, which specializes in the development and sale of sustainable engineering plastics based on post-industrial and post-consumer raw materials. In his role, he is responsible for the strategic direction and operational business of the company. He has also been involved in the development of pioneering recycling/compounding technology.
Hartmut Schoon completed his academic education from 1985 to 1989 with a degree in Electrical Engineering - Automation at the Wilhelmshaven University of Applied Sciences. He then completed his degree in technical business administration. From 1989 to 1997, he worked as a planning engineer for the chemical and petrochemical industry. From 1998 until the founding of Enneatech, he was Managing Director of the plastics recycling company Poly-Beek Kunststoffe GmbH & Co.KG.
Talk: Digital Self-Sovereign Product Passport
Jonas Kallisch OFFIS Institute for Information Technology
Abstract: The digital product passport presents many companies with the challenge of making more information available in the future on how their products can be manufactured and, if necessary, repaired. The problem for many manufacturers is that the data to be made available allows conclusions to be drawn about the production processes and can therefore reveal intellectual property. For small and medium-sized companies in the manufacturing sector in particular, however, this intellectual property represents a key competitive advantage that they cannot do without. One solution could be the use of data sovereignty-preserving processes such as federated learning. This could create a digital but sovereign product passport that takes into account the interests of both manufacturers and consumers.
Speaker Bio: Jonas Kallisch has trained as an IT specialist for application development. He worked at Rheinmetall Defense Electronics from 2009 to 2014. He then worked for the in-house SAP consultancy of the CEWE Foundation during his Bachelor’s and Master’s degrees. He has been a research assistant since 2018 and is investigating the digitalization of production systems.
Talk: Decentralized Transparency: Blockchain as the Key to Sustainable Supply Chains
Tobias Jornitz Fraunhofer IML
Abstract: In our presentation, we will shed light on the central role of blockchain technology to enable traceability and transparency in supply chains. The presentation will further highlight the potential of a blockchain-based blueprint for digital product passports (DPP) and outline dedicated benefits for companies using DPPs by providing insights into current research projects.
Speaker Bio: Tobias Jornitz is an experienced research associate at the Fraunhofer Institute for Material Flow and Logistics (IML) for over 7 years with a sound background in procurement and supply chain management. His research focuses on sustainable and resilient supply chain design enabled by technologies such as Blockchain and AI.
Talk: Digital Product Passport as the Cornerstone of Circularity
Steffen Bölling Fraunhofer IML
Abstract: The Digital Product Passport (DPP) is becoming a central tool for enabling regulatory compliance, supporting digital transformation, and unlocking new business model potentials, especially in the skilled trades sector. For many craft enterprises, the path toward a DPP begins with foundational steps such as digitizing documentation, standardizing product data, and understanding circular requirements. These efforts not only address upcoming regulatory demands but also prepare companies for a broader digital transition. This talk highlights the current state of DPP-related activities in the skilled trades, showcasing how small and medium-sized enterprises can actively participate in pilot projects, shape future standards, and develop service-oriented approaches. The presentation offers insights into practical use cases and strategic pathways to integrate DPPs into craft-related processes and ecosystems.
Speaker Bio: Steffen Bölling is an industrial engineer with a Master’s degree from the Technical University of Dortmund and has been working at the Fraunhofer Institute for Material Flow and Logistics (IML) for over four years. His specialist focus is on the digitalization of the skilled trades, in particular the development of digital solutions and business models. A particular focus of his work is the digital product passport and the design of service-oriented ecosystems to promote digital transformation in small and medium-sized enterprises.
IF Session 3: Production from Europe
Wednesday, 14th May 2025, 13:00–15:00
Chair: Jerker Delsing
Session Theme: Europe stands for high-quality, sustainable, and technologically advanced production. This session is dedicated to Europe’s role as a global industrial location and highlights how regional strengths, innovative ecosystems, and strategic cooperation ensure competitiveness. Learn about successful examples where European values such as quality, responsibility, and resilience meet modern production technologies. Discuss with experts which political, economic, and technological courses must be set for a strong European industry.
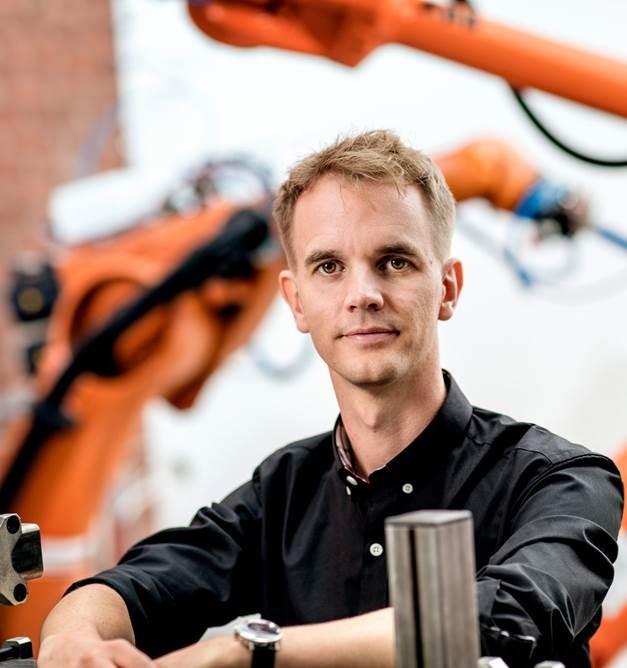
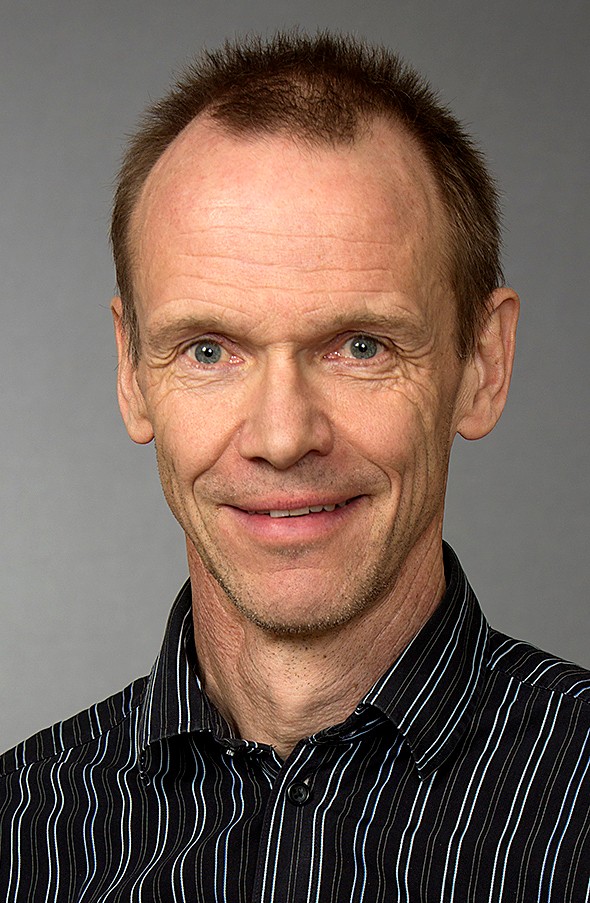
Talk: Industrializing Intelligence: When smart gets real
Kristofer Bengtsson Volvo Group
Abstract: For nearly two decades, I’ve worked in research to develop intelligent automation systems and smart operations. Over the past five years, however, my focus has shifted toward bridging the gap between academic research and industrial reality. In this keynote, I’ll share that journey – from exciting breakthroughs to long, difficult nights; from wrestling with enterprise IT to the joy of writing Rust code in our embedded controllers. A central part of the story is our work on a technology we call GPSS: Generic Photo-based Sensor System. GPSS is an automatic transport system that combines simple transport robots with fixed ceiling-mounted cameras for navigation and obstacle detection. By running real-time semantic segmentation inference on a Kubernetes cluster, we’re able to detect obstacles such as human workers and other vehicles, and with that input, control a fleet of robots. Our focus has been on making the system scalable across all our plants, ensuring it can be installed, trained, and operated locally while maintaining robustness and simplicity. The goal has been to keep it simple and make it smart only when necessary.
Speaker Bio: Kristofer Bengtsson received a Ph.D. degree in signals and systems from Chalmers University of Technology, Gothenburg, Sweden, in 2012. From 2001 to 2005, he was with Advanced Flow Control AB, developing control systems and user interfaces, and from 2005 to 2011, he was with Teamster AB, Gothenburg, an automation firm. He was an Associate Professor in the automation resource group at Chalmers until 2022 and is now a senior researcher in Smart and Connected operations at Volvo Group. His current research interest includes AI and edge communication and computing, energy optimization of automation systems, online planning architectures for intelligent automation systems, as well as supporting operations with online prediction, planning, and optimization.
Talk: Software-defined CPS
Olov Schelén Xarepo AB
Abstract: Innovative software from SMEs plays a crucial role in the cyber part of industrial CPS. This talk will cover challenges, opportunities, and directions in software development, virtualization, and modeling to support the planning of industrial processes and the integration of distributed CPS. The objectives include customer-focused and efficient engineering, deployment, and operation. This encompasses the engineering tools and AI support needed for development and to provide continuous updates and upgrades in the operational environment. A use-case example is presented where general observations may be extrapolated into a future vision.
Speaker Bio: Olov Schelén is the CEO and a founding partner of Xarepo AB, an SME focusing on software development and services. He is also a professor at Luleå University of Technology (LTU), where he teaches and supervises PhD students on topics in distributed computer systems and cyber-physical systems.
Talk: Culture Change in Swedish Industry vs Digital Transformation
Erik Molin Swedish Industrial Interoperability Association (SEIIA)
Abstract: We see that the industry is not adopting a new way of working. The use of digital solutions and digital information exchange services based on standards is lagging behind, and from a Swedish view, we need to speed up the work and adopt modern methods and ways of working. There are several good examples that we could have a continuous flow of information in an asset lifecycle, but it relies on the fact that we have a common digital language in our asset management systems that makes the lifecycle interoperable. The biggest threat to the change that we need to make is not standards, methods, and systems. It is people! Today, we get rewards when we don’t extend the budget and make the new physical asset in place in time and with the right outcome. That’s important, of course, but if you look at the lifecycle cost, is it optimal? Often, the project delivery is document-based, and a lot of information is locked in PDF files and different CAD files. When the industry later wants to make maintenance and updates, the problem starts, as the document-based information is difficult to update and keep in good shape. Important maintenance data are not available in an easy-access tool (kept in the PDFs). The new way of working is based on digital information exchange, and documents are being replaced in many areas with visualisation. The problem is that this is not the way the work has been done, and the management is not pleased when the project management for the first project can’t say that they have secured the budget, and the timeline is safe. And the risk is that the instructions for new projects will be “business as usual”. In SEIIA, the analysis of this situation is that companies and asset owners need to work with the change management. The top management needs to realise that the organisation needs to learn and test new ways of working, and the first project will have outcomes other than the traditional ones. To be agreed that the new way of working is the future. That is to invest in new knowledge and a digital platform that will be profitable in the future, where maintenance data is in place from day one in the asset management system. The production and maintenance have all the necessary data and information in place, and the update will be done online in real time. To prove this culture change, we are running a national project in Sweden called “Digitala Stambanan” Phase 3, Best Practice. We arrange several workshops where we invite different stakeholders in the whole lifecycle, we collect the inputs, and later in the project, we do a demonstration where we want to show that the New Way of Working is realistic and available now.
Speaker Bio: Erik Molin: I’m an electric and process automation engineer, and I have worked in the process industry since the late 80s. The last 20 years I have got a focus on how industry could have a better information exchange through the life cycle of a process industry. The last 6 years I have been involved in the startup of the Association SEIIA as the Operations manager, and today we have more than 40 members in the association. I am passionate about solving the challenges facing the industry and working to ensure that digital transformation creates an efficient and profitable industry in the future.